Eanos experiments with casting
(This is a thread from Mizahar's fantasy
role playing forum. Why don't you
register today? This message is not shown when you are logged in. Come roleplay with us, it's fun!)
This shining population center is considered the jewel of The Sylira Region. Home of the vast majority of Mizahar's population, Syliras is nestled in a quiet, sprawling valley on the shores of the Suvan Sea. [Lore]
by Eanos on November 25th, 2013, 11:29 pm
With the wax model carefully laid aside he could turn his attention to the creation of the mould. For this he would be making a sand cast in a two part mould, since these were easily available in the Ironworks. He selected the mould, sand and moulding tools that he would need and returned to his bench.
The frame was metal on this mould but it just as easily could have been wood since he was working with brass and the heat would not be high, or come to that a one off clay mould would have sufficed for the lost wax method, but it was easier to work with the tools at hand and worry about improvising at another time when it was necessary.
He filled the base with slightly damp sand nearly to the top and firmed it down so that there would be no air gaps. He then placed the wax pattern in place and filled in around it with sand which he then firmed gently. It was at this point that he needed to consider exactly how the metal would run down into the mould and to fill the gaps left by the wax once it had been removed. For the metal to flow into the shape then it was necessary that he planned the route it would follow to ensure that there were no dead ends which would fill with air with nowhere to go and block that part of the pattern from filling with metal. That air needed somewhere to go, so he planned that too, placing chalked wooden rods into the sand to create channels then he completed filling the base with damp sand, tamped it down and chalked over the surface.
Then he fitted the top part of the pattern and put in place the wooden dowels and plugs that would allow the metal to enter and the air to escape and filled it with sand which he also tamped down level. The next part was the most tricky for he now needed to gently separate the two halves of the mould to remove the wooded dowels.
He held his breath as he carefully lifted the top up. If he’d tamped it down well enough it would come away cleanly. If the sand was too dry it would collapse, if too damp then it would stick. He was lucky that it came away reasonably cleanly so that he could simply remove the wooden dowels. Next time, he told himself, he would try the advice that he’d been given which was to use wax in place of the wooden dowels so that he would not need to separate the frames, and that was advice that he now appreciated the wisdom of, though he imagined with practice it would become simple enough.
With the frames locked together and the wooden plugs removed from the top section it was time to place the mould somewhere hot enough for the wax to melt and vapourise. If any was left in the pattern then he would have to hope that the hot metal would flash vapourise it cleanly enough that it wouldn’t be a problem.

-
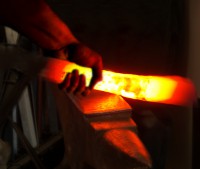
Eanos - Overgiven Magesmith
-
- Posts: 535
- Words: 443521
- Joined roleplay: March 22nd, 2010, 2:38 pm
- Location: Syrilas
- Race: Isur
- Character sheet
- Storyteller secrets
- Plotnotes
- Medals: 4
-
-
by Eanos on November 26th, 2013, 8:35 pm
As that was heating so too did he put two small brass bars into the casting pot and set it to heat in the furnace. He kept an eye on the mould as it dried a little and he hoped that the wax evaporated fully.
Once more he was waiting for the bars to melt but he had plenty of patience and pumped the bellows to push more air through and raise the temperature even higher. Slowly the brass bars softened and then melted and he stirred them once more with an iron rod to ensure that the metals were fully melted and the alloy was properly mixed.
When he was happy that it was ready then he lifted it out and took it over to where the casting frame stood and making sure that both the inlet and the vent were clear he started to pour the brass down into the inlet. The metal hissed and spat a little and steam rose out of the vent which indicated that indeed some wax had still been left in there. He tapped on the rim of the mould as he poured with his other hand so that the vibration would help the molten metal flow down and get past any trapped air, and for the air to pass out of the metal and make its way out of the air vent.
There was a little more smoke and steam from the vent and then a glimmer of metal appeared there at the same time as the flow into the inlet started to back up and pool. He continued to tap for a moment and then left the mould to cool, pouring out the remainder of the molten brass in the casting pot back into a tray where it could later be reused.
The waiting was the hardest part for he was impatient to see what the result might be and if the guard had been cast properly. There was an element of excitement as he waited for it would be a long time since he had done this. His fingers tapped impatiently on the mould and he watches as the metal in the plug slowly changed colour the surface become duller in colour. Still it was hard to wait for he needed the metal to solidify properly down in the heart of the mould where the sand would act as an insulator and if he acted on his impulses then the metal might not be properly set within its case of sand.
He waited longer but then could restrain his curiosity no more. Unlocking the frames he took the top frame off and the sand within now dry crumbled and flowed over the edges of the bottom frame. He wiped it away carefully from around the brass inlet and vent and then started to uncover the guard itself. Finding that it was in fact solid he dug his finger into the sand and lifted out the whole assembly of guard and runners, shaking the bulk of the sand free.
He could see immediately that there was a fault, a section of the guard which had not formed and he frowned at it, disappointed but in his heart not overly surprised by the failure. Setting it on the workbench and ignoring the sand which spilt over it he traced the lines of the runners and quickly realised that there was one missing. One of the runners had collapsed he surmised, leaving the air nowhere to go and blocking the brass from flowing through that section. He tossed the metal aside not bothering to break out the faulty guard no matter that his work had been wasted. It was a valuable lesson for next time and now he set to clearing up the mess so that he could start again.

-
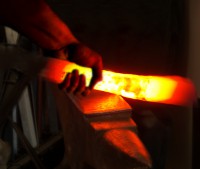
Eanos - Overgiven Magesmith
-
- Posts: 535
- Words: 443521
- Joined roleplay: March 22nd, 2010, 2:38 pm
- Location: Syrilas
- Race: Isur
- Character sheet
- Storyteller secrets
- Plotnotes
- Medals: 4
-
-
by Eanos on November 27th, 2013, 9:58 am
With the failure of the brass casting Eanos knew that he needed to try again, but he was not dismayed by it. There were lessons in what he’d done, some of which he had identified and would attempt to rectify. Other lessons would remain unlearnt for he had not the skill to recognise th problems and those would remain until he had the skill to identify them.
If he had any sense then he knew that what he ought to do was to repeat the exact process until he was successful and that was certainly what he would insist that any apprentice he was supervising would have to do. However, not being an apprentice as such for all that he lacked skill in this, Eanos was free to go with his ambitions on this.
For his next attempt at casting he intended to use the bronze, for no more real reason than that of curiosity about how the metal would react when heated and poured as opposed to how the brass had reacted. Casting for him was still something of a curiosity, though he had some very specific applications for it in regards to weapon fittings, but at this point he was far more interested in the alloy aspects of it.
He toyed with the lump of wax and wondered if he was overlooking possibilities here and so he stopped for a moment to explore the thought. He had experiments still in mind with regards steel and the decoration of it, both in terms of the insertion of precious metal wires and in the welding in of steel wire. Both of these tingled in his mind as a way forward in terms of the melding of magic and smithing but as yet he had not found the key that he sought. Somewhere in mis mind was the application of magic to small parts of the weapon whose overall impact was much larger, though he was aware of the limitations of magecraft in this respect. Could he use casting to the same effect? Was it possible to cast two metals together? He could see no reason why not, or again he could use the same techniques to decorate a cast metal as he could a forged one.
He was no further forward except that he was now sure that there was value in mastering the skills of casting as well as those of alloying. He put the thought aside and took up the carving tools. He was realistic enough not to worry about attempting to decorate this piece, he merely wanted to attempt a three dimensional piece and in this case the end cap for a hilt. It’s exactly shape didn’t matter as it was purely a test and as much as anything else it was a test of his ability to carve the wax without the heat of his fingers melting it or his fingers crushing the delicate form accidentally.
He managed to pass that test and so moved on to the task of creating the sand case once more, this time building a more extensive system of runners to allow the air to move away and making them in wax so that he would not need to disturb the form in order to remove any parts. He worked carefully for this would be but the first of many attempts before he was happy with his ability to make this work.

-
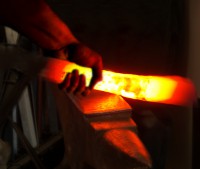
Eanos - Overgiven Magesmith
-
- Posts: 535
- Words: 443521
- Joined roleplay: March 22nd, 2010, 2:38 pm
- Location: Syrilas
- Race: Isur
- Character sheet
- Storyteller secrets
- Plotnotes
- Medals: 4
-
-
-

Radiant - Sailor Radiant
-
- Posts: 2195
- Words: 781936
- Joined roleplay: July 2nd, 2013, 1:39 pm
- Location: DS of Syliras
- Race: Staff account
- Office
- Scrapbook
- Plotnotes
- Medals: 2
-
Users browsing this forum: No registered users and 0 guests